Quality Without Compromise
We have access to the best manufacturing network in the world. Used extensively at the highest level of the aerospace, motorsport, medicine and maritime industries we give access to previously exclusive manufacturing partners.

Industry Leading Quality

350+ Manufacturing Partners

Carbon Offsetting

Quick Delivery
Manufacturing Capabilities
Working closely with our expert manufacturing partners we have access to the best manufacturing network in the world. Used extensively at the highest level of the aerospace, motorsport, medicine and maritime industries we give access to previously exclusive manufacturing partners.
Not only does this ensure the best quality products but also gives you the best possible price for your designs.
The minimum requirement for inclusion in our partner network is the possession of ISO 9001 certification. This globally recognised standard ensures that our partners maintain rigorous quality management systems, guaranteeing consistency, reliability, and continuous improvement in their manufacturing processes.
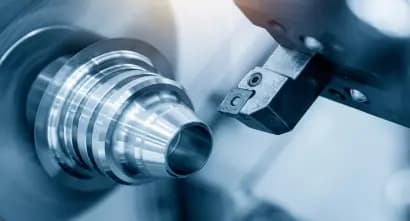
CNC Turning
50+ Material options
3,4 & 5 Axis milling available
Tolerances as tight as +/- 0.01mm
Surface from finishes to roughness up to Ra0.8μm
Extensive heat treatment, Coating and Inspection options
Turning lengths up to 2m
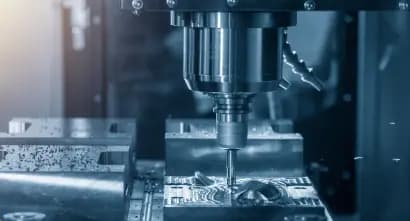
CNC Milling
50+ Material options
3,4 & 5 Axis milling available
Tolerances as tight as +/- 0.01mm
Surface from finishes to roughness up to Ra0.8μm
Extensive heat treatment, Coating and Inspection options
Coming Soon
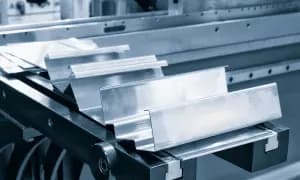
Sheet Metal
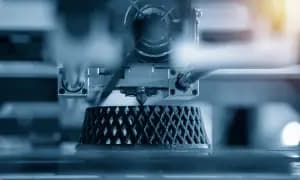
3D Printing
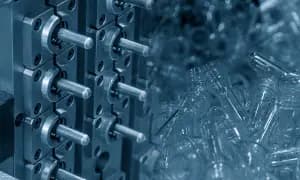
Injection Moulding
Engineering
Rotational Machining: CNC turning involves rotating the workpiece while a stationary cutting tool shapes it, making it ideal for creating cylindrical parts like shafts, rings, and pipes.
High Precision: CNC turning provides high precision and tight tolerances, allowing for the production of accurate and consistent parts across multiple runs.
Efficient Production: CNC turning is highly efficient for producing parts with symmetrical features and is often used for high-volume production runs due to its speed and repeatability.
Versatile Material Handling: Like CNC milling, CNC turning can work with various materials, including metals, plastics, and composites, making it suitable for diverse industries.
Automated and Programmable: CNC turning machines are controlled by CAD/CAM software, enabling automated operations and reducing the need for manual intervention while ensuring consistent quality.
Precision Machining: CNC milling uses computer-controlled machines to precisely cut and shape materials, producing highly accurate and complex parts.
Versatility: Capable of working with a wide range of materials, including metals, plastics, and composites, CNC milling is used in various industries such as aerospace, automotive, and medical.
Subtractive Process: CNC milling is a subtractive manufacturing process where material is removed from a solid block (workpiece) using rotating cutting tools to create the desired shape.
Automated Control: CNC milling machines are programmed using CAD/CAM software, allowing for automated and repeatable production with minimal human intervention.
Multiple Axes: CNC milling machines typically operate on 3 to 5 axes, enabling them to create complex geometries and intricate features in a single setup.
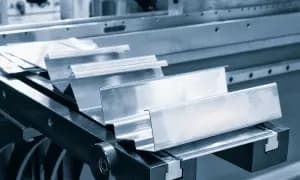
Coming Soon
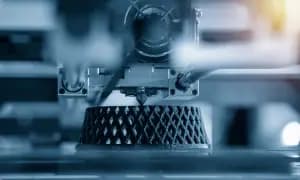
Coming Soon
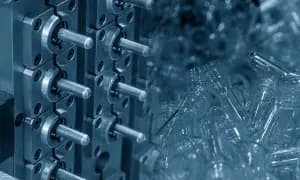
Coming Soon
Quick to machine.
Impressive strength-to-weight ratio.
Limited corrosion resistance.
High conductivity.
Easy to recycle but energy-intensive to produce.
Very strong.
Great strength-to-weight ratio.
Excellent corrosion resistance.
Brilliant biocompatibility.
Raw material production is highly energy-intensive.
Cheap to purchase.
Easy to machine.
Tensile and yield strengths are low.
Susceptible to rusting.
Can be recycled, and production entails relatively low energy consumption.
Good strength properties; some grades provide incredible strength.
Excellent corrosion resistance.
More expensive to buy and machine.
Has a long lifespan.
Easy to recycle.
Offer a wide range of properties, from high strength and chemical resistance (like PEEK) to low-cost options (like ABS), making them suitable for diverse CNC milling applications.
Easy to machine
Are much lighter than metals, ideal for weight-sensitive applications.
Many plastics are recyclable, with growing options for eco-friendly materials.
Faster machining and lower material costs make plastics economical.
Precise machining capabilities.
Can be difficult to machine due to high flexibility to toughness.
Highly conductive.
Production of raw material is energy-intensive.
Recyclable without any real loss of performance.
Brilliant corrosion resistance against seawater.
Low strength properties, so best employed on low-stress components.
Easy and cheap to machine.
A low-friction metal, so good for bearings.
Recycled consistently and effectively.
As a soft metal, it is cheap to machine.
Good corrosion resistance.
Highly conductive.
Can be tarnished and isn’t great for bending.
Significant environmental advantages compared to other metals.
This is our standard finish, ensuring the removal of all burrs and eliminating any sharp edges. There are no additional costs or processes involved, resulting in the fastest delivery times.
Delivers the smoothest finish for the metal. Offers an excellent aesthetic look and feel. However, it is time-consuming, which leads to increased manufacturing costs.
Provides some corrosion resistance to less extreme environments.
Serves as a low-cost alternative to hard and chromic anodizing.
Has the lowest carbon footprint and is the most recyclable coating option.
Limited materials accept powder coating, and the coating can fade over time.
Thickness buildup ranges from 100µm to 200µm, and thickness is difficult to control.
Low friction, lubricating coating that helps prevent galling.
Cannot flake off material as it is integral to the metal.
Finish is a blue/grey color.
Increases your costs and carbon footprint due to additional manufacturing processes.
Thickness buildup is 0.01µm.
Provides good corrosion resistance for harsh environments.
Can flake off material as it is not integral to the metal.
Helps with durability but not as much as hard anodising.
Does increase your costs and carbon footprint due to additional manufacturing processes.
Thickness buildup is 5µm.
Provides excellent corrosion resistance for harsh environments for up to 20 years.
Mainly benefits by offering corrosion resistance to aluminum.
Can be used decoratively for metals such as stainless steel and titanium in multiple colors.
Does increase your costs and carbon footprint due to additional manufacturing processes.
Thickness buildup ranges from 25µm to 100µm.
Provides critical inspection of key dimensions.
Suitable for standard checks, which encompass most components.
Human error can occur.
Cost is relatively low.
Provides very accurate data.
Reports are provided with delivery.
Costs are mid-range.
Requires electricity, which increases your carbon footprint.
The most accurate inspection process on the market.
Scan provided with delivery.
Costs are high due to expensive equipment and highly skilled operators.
Requires significant electricity, which increases your carbon footprint.
Improved Mechanical Properties: Heat treatment can alter the physical properties of a material, including its hardness, strength, flexibility, and toughness. This enhancement makes the material more suitable for specific applications or manufacturing processes.
Enhanced Wear Resistance: Heat treatment can impart wear-resistant characteristics to the surface or bulk of a material, improving its resistance to abrasion, erosion, and other forms of wear.
Reduced Brittleness: Certain metals may exhibit weakness or brittleness under certain conditions. Heat treatment can mitigate this issue by enhancing the material's toughness and resistance to brittle fracture.
Stress Relief: Heat treatment can alleviate internal stresses within a material, facilitating easier machining or welding. This minimizes the risk of distortion and cracking during subsequent processing or service.
Tailored Treatments for Steel: Heat treatment is especially advantageous for steel materials. It can be applied during manufacturing processes such as hot forming or post-welding to optimize the material's properties and performance.
Distortion: Heat treatment has the potential to induce distortion in the material, particularly when there are variations in cooling rates or uneven heating. This distortion can impact the dimensional accuracy and shape of the part.
Surface Oxidation or Contamination: Some heat treatment processes involve exposure to air or specific atmospheres, which can result in surface oxidation or contamination. This may diminish the material's surface finish or introduce unwanted impurities.
Increased Costs and Carbon Footprint: Heat treatment processes can incur additional expenses in the manufacturing process. These expenses encompass equipment costs, energy consumption, and the requirement for skilled personnel to execute the treatment.
Tolerancing is employed to ensure that your components fit their mating parts and are immediately ready for use.
We offer a range of options from ±0.01mm to ±1.00mm.
It's crucial to utilize geometrically stable materials when precise tolerances are necessary.
The narrower the tolerance, the greater the manufacturing, measurement, and quality assurance costs.
Additionally, tighter tolerances result in a higher carbon footprint.